宝马莱比锡工厂作为宝马公司在德国技术最先进、环保和可持续发展都走在最前列的汽车工厂,可以看作是最具4.0工厂味道的代表之一。
宝马莱比锡工厂因在精益管理方面的卓越成就,多次荣获德国及欧洲权威机构颁发的“精益和绿色管理奖”和“最佳工厂”等奖项,这些都得益于莱比锡工厂在灵活生产、可持续资源利用、企业精益管理等方面的持续创新。
在宝马始终提供高品质产品的背后,正是有一套高效灵活的生产物流体系作为支撑。该工厂经理表示“宝马永远是为客户及自己的员工着想,质量永远是我们的最高优先级”。从2014年7月开始,莱比锡工厂开始1系和2系车型串行生产,有时候,更是需要1系、2系和X1多款车型在一条生产线混合生产。由于宝马莱比锡工厂繁忙的业务需求,
工厂人员近年来持续增加。2014年7月,莱比锡工厂共有4000名员工,其中1400名都是2011~2014年新加入的。
标准化、模块化和数字化的产品设计是实现工业4.0的基础,这一点在宝马莱比锡工厂能够得到充分印证。宝马1系和2系车型同属一个平台,为此可以共用同一生产线,且装配时的大部分组件也是通用的。通过选配不同模块(如汽车电子单元)、不同车体颜色,灵活生产出满足不同客户需求的差异化车型,让模组的数量大大简化。而实现小批量、多品种定制化混线生产的重要前提就是标准化,同样,模块化和数字化为此生产模式提供了更多可能。
正因为如此,宝马莱比锡工厂目前不仅能做到多种车型按订单生产和混线生产,还能在不损失生产节拍和品质的前提下,实现每台下线车型都能满足大规模定制的市场需求,即每一台宝马
汽车可以根据客户的意愿生产出来,这一点很符合工业4.0的特性之一。
莱比锡工厂的物流创新
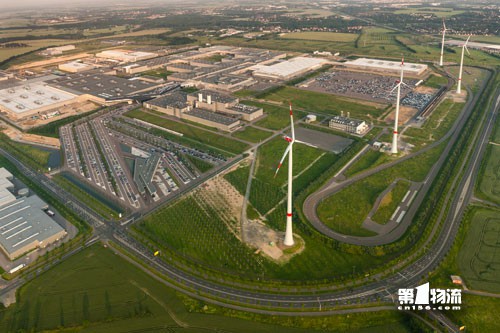
宝马德国莱比锡工厂
宝马莱比锡工厂的整体设计思路十分创新,作为核心的中央大楼因其设计创新性而荣获2005年德国建筑奖。为能灵活应对未来需求,宝马在莱比锡设计出了最可持续和高效灵活的生产与物流模式。与中国传统的标准厂房设计不同,围绕中央大楼建设的三大核心生产区域(即车身车间、喷涂车间和总装车间)呈现出不规则排列。
贯穿占地面积40000 m2的中央大楼核心区域天花板上方的是一个空中走廊,其由一个有600台输送机的悬挂式输送系统组成,主要用于连接焊装、涂装和总装3个车间。该系统可将原始车身从车身车间输送到车身仓库,再送至喷涂车间,之后再将其送回车身仓库,最后从车身仓库送至总装车间。另外,车身仓库被设计为一个混装仓库,已喷涂车身和原始车身都被暂存于此。
鉴于车身穿梭于空中走廊的创新设计,使得主要办公区和生产车间两者能够相互渗透、融为一体,让工厂整体感更强,甚至在员工食堂和会议室也能看到实时的车身输送过程和订单不同阶段;这让各生产区域之间实现了高效互联,使车身输送过程做到一览无余。由此,
宝马的工程师们可以在车间或是走廊、甚至餐厅的任何地方,实时跟踪订单状态,及时发现和调整生产进度,让人与工厂实现完美融合。
在莱比锡工厂,每天约有一万立方米的材料被输送至各个生产环节,为确保物流的高效、精益、低库存,所要运输的材料必须在正确时间以正确的顺序到达相应地点,这就需要高效精准的物流系统以及和供货商之间的密切配合。
宝马的生产计划主要按照客户订单来制定,零部件供应商会按照生产订单按序供货,供应商与生产之间的JIT生产模式,也因总装车间独特的梳状结构建筑设计得到更加充分的实施。运送不同零组件的货车可直接开至离装配线最近的区域,部件进厂后可直接送至相应工位完成组装,与先入库再二次配送上线的传统物流方式相比,节省了大量库存和不必要的作业时间。这种创新的物流模式,不仅缩短了生产和物流供应的距离,也为未来的生产线扩展、引入新技术打下了良好的基础,以最小的投资成本实现高效集成。